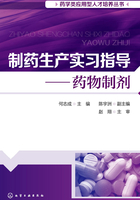
第一章 厂区和车间概述
第一节 厂区概述
药品生产企业总体布局包括两个方面:一是指洁净厂房工厂与周边环境的布置,即选址;二是厂区所有建筑物、构筑物、道路、运输、工程管线等设施的平面布置规划。药品生产企业对厂房设施的合理设计,直接关系到药品质量,乃至人们生命安全。
一、选址
医药工厂厂址一般位于大气含尘、含菌浓度低,无有害气体,自然环境好的区域。远离铁路、码头、机场、交通要道等,无明显异味;无空气、土壤和水的污染源、污染堆等。如不能远离严重空气污染区时,则位于全年最小频率风向下风侧。
药品生产企业总体布局应符合《化工企业总图运输设计规范》《建筑设计防火规范》《石油化工企业设计防火规范》《药品生产质量管理规范》(2010年修订)等相关规范。
二、企业总体布局的基本原则
①厂区可分为行政区、生产区、辅助区和生活区。
②厂区主要道路应贯彻人流与物流分流的原则,做到“各行其道”,尽量避免交叉污染,人流物流不穿越或少穿越,并应考虑产品工艺特点,合理布局,间距恰当,内外运输相协调,线路短捷、顺畅,避免或减少折返迂回运输。
③医药工业洁净厂房人流出入口和物流出入口宜在厂房不同方向设置。
④洁净厂房周围道路面层材料整体性好,发尘少。
⑤医药工业洁净厂房周围设置环形消防车道,也可沿厂房的两个长边设置消防车道。
⑥医药工业洁净厂房环境清洁,洁净厂房周围绿化。露土面积少,不种植对药品生产有不良影响的植物。
⑦兼有原料药和制剂生产的药厂,原料药生产区位于制剂生产区全年最大频率风向的下风侧。高致敏性药品(如青霉素类)或生物制品(如卡介苗或其他用活性微生物制备而成的药品)必须采用专用和独立的厂房、生产设施和设备,其生产厂房位于厂区全年最小频率风向的上风侧。
三、厂内生产区域的划分
药厂内通常包括生产区、原辅料包材仓储区、成品仓储区、质检研发区、动力区等。生产区应当有适度的照明,目视操作区域的照明应当满足操作。生产区内可设中间控制区域,但中间控制操作不得给药品带来质量风险。仓储区的设计和建造应当确保良好的仓储条件,并有通风和照明设施。仓储区应当能够满足物料或产品的贮存条件(如温湿度、避光)和安全贮存的要求,并进行检查和监控。生产区和原辅料包材仓储区、成品仓储区应当有足够的空间,确保有序地存放设备、物料、中间产品、待包装产品和成品,避免不同产品或物料的混淆、交叉污染,避免生产或质量控制操作发生遗漏或差错。质检研发区通常应当与生产区分开,生物检定、微生物和放射性同位素的实验室还应当彼此分开。
四、车间生产区域的划分
(1)一般区
一般区为产品或物料不明显暴露操作的区域,如外包装区、总更衣区、车间动力区域(空调、制水、空压、制冷、真空、配电等)该区域内对空气洁净度通常没有要求。
(2)D级洁净区
口服液体和固体制剂、腔道用药(含直肠用药)、表皮外用药品等非无菌制剂生产的暴露工序区域及其直接接触药品的包装材料最终处理的暴露工序区域,应当参照“药品无菌药品”附录中D级洁净区的要求设置,企业可根据产品的标准和特性对该区域采取适当的微生物监控措施。
(3)无菌区
无菌药品生产所需的洁净区可分为以下4个级别:
①A级:高风险操作区,如灌装区、放置胶塞桶和与无菌制剂直接接触的敞口包装容器的区域及无菌装配或连接操作的区域,应当用单向流操作台(罩)维持该区的环境状态。单向流系统在其工作区域必须均匀送风,风速为0.36~0.54m/s(指导值)。应当有数据证明单向流的状态并经过验证。在密闭的隔离操作器或手套箱内,可使用较低的风速。
②B级:指无菌配制和灌装等高风险操作A级洁净区所处的背景区域。
③C级和D级:指无菌药品生产过程中重要程度较低操作步骤的洁净区。
无菌药品的生产操作环境可参照表1-1、表1-2中的示例进行选择。
表1-1 最终灭菌产品生产操作相应洁净级别示例

①此处的高污染风险是指产品容易长菌、灌装速度慢、灌装用容器为广口瓶、容器需暴露数秒后方可密封等状况。
②此处的高污染风险是指产品容易长菌、配制后需等待较长时间方可灭菌或不在密闭系统中配制等状况。
表1-2 非最终灭菌产品生产操作相应洁净级别示例

①轧盖前产品视为处于未完全密封状态。
②根据已压塞产品的密封性、轧盖设备的设计、铝盖的特性等因素,轧盖操作可选择在C级或D级背景下的A级送风环境中进行。A级送风环境应当至少符合A级区的静态要求。